The Building of the Goose
December 2014 to April 2015
I was not going to build a Goose. I was done with box boats after
the 2014
Texas 200. Then I saw a couple
videos of Ian Henehan sailing his Goose at over 12kts and decided
maybe I'd better give it a go.
There is a lot to be said for box boats. No, they are not "boaty"
shaped or all that aesthetically pleasing, but they are very (very)
stable, carry a LOT of crew or cargo, and they go like stink on
ice. From a building standpoint, they are very easy to build and
they make very good use of the materials - not nearly as much waste
as when building a pointy boat.
Practicality won out, and so we started.

The shape: Not all that pretty, but prettier than a box boat has
the right to be. This is another reason I like the Goose design:
Like it's ancestor, the Puddle
Duck Racer, you can do anything you want with the topsides and
sails - builder's choice, designer's dream.
Note: We are starting with an external leeboard simply to
provide more space in the cockpit. There is every probability we'll
go to an internal daggerboard some time in the future.

Mik Storer, the primary
designer of the Goose, advised me to "Build LIGHT" which
I had every intention of doing, until I saw this Alowood
at the local Bargain Barn. I first noticed it was knotless - all
5/4 x 6 x 10 feet of each stick. Then I noticed the beautiful red
color. Lastly, I noticed the weight, which is more than good old
Doug Fir - but it was PRETTY! I went with Alowood.
Normally, people start building the hull of the boat first - they
get the big part done, then get bound up in the minutia of all the
fiddy bits as they try to get their boat into the water. I was going
the other way - starting with the fiddy bits - the mast and spars,
in particular.

The original sticks were only ten feet long, so I had to scarf
the spars and the parts for the mast. Nothing is more fun than making
wood longer.

Patience and Connie came by the Boathouse and got pressed into
helping me assemble the mast. It is a hollow box that tapers as
it goes up - it's good to have helpers.

After the epoxy cured, I took my favorite sander with a 36 grit
belt to it to smooth out the joins.

A 3/8 roundover bit makes the corners nice and smooth. I should
probably get a 1/2" roundover

Is Alowood strong enough for a mast? Well, it held me up, so that
is plenty strong.

Mast and spars shaped, it was time to turn to on the foils - the
rudder and leeboard. I liked how the Alowood looked, and I had some
Mahogany that had been donated to us, so I started doing Alowood/Mahogany
glue-ups.

12" power planers are NICE.
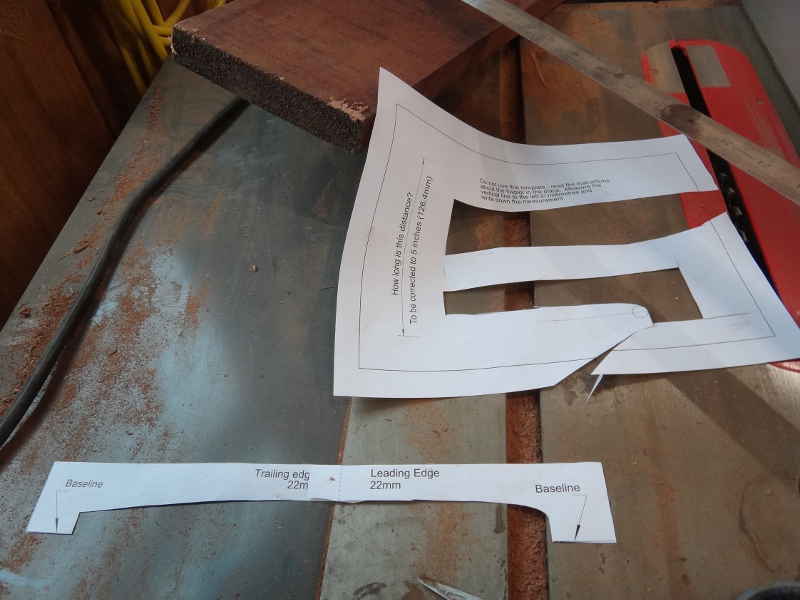
Mik is pretty particular about his foil shapes, so I made a template
to help me out.

(out of sequence) Midnight Mike came down from Astoria and varnished
the mast, spars, and foils.

(out of sequence) Oh, those are PURTY!

Next was making a piece of plywood 12' long. I used Dynamite Payson's
method of fiberglass on both sides.

Speaking of sides, it was time to work on them as well. Abby had
stopped by, so I had her help me out. The sides are made out of
1/8" (4mm) ply.

There is a slight reverse sheer on the sides - a small
sheer, only rising 2", peaking at the 5' mark from the stern.
I want to be able to row this boat comfortably but I don't want
too much freeboard. Also, rather than have full length airboxes,
I freed up the middle for storage, there'll still be plenty of flotation
in the ends.

The sides are 4mm while the bottom and transoms are
6mm. Everything is framed in with 1x1 Doug Fir.

Bob D. came by for a visit while I was coating the
internal surfaces with epoxy. It gets hard to coat them once everything
is together. Those bare spots are the cutouts on the internal bulkheads
- no reason to waste epoxy on those.
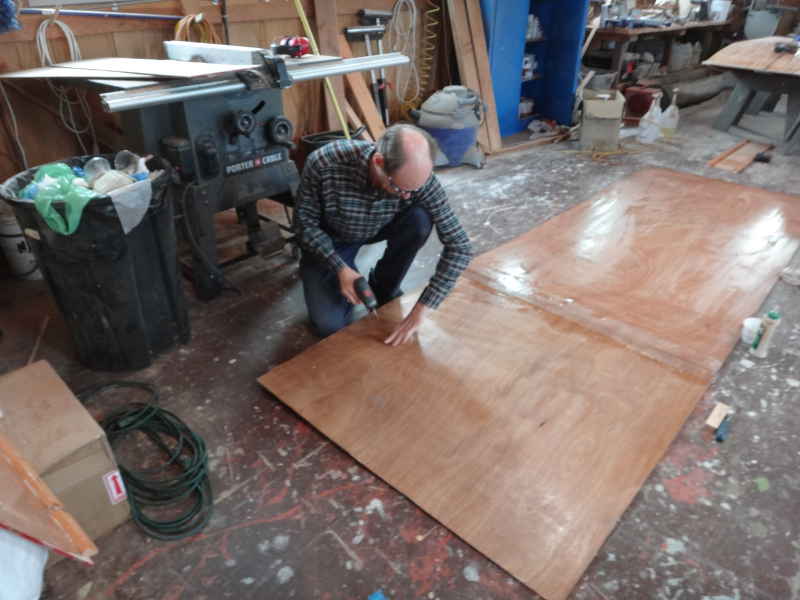
We were getting ready to go 3D - pre-drilling pilot
holes for the screws.

Here we go - sides attached to the transoms, bottom
ready to go.

. Goose sailboats get their hull number based on the
date they go 3D, and this day was January 31, 2015. Hull numbers
are done in the YYMMDD format, so we got 150131, which is prime.
Auspicious? I'd say so.

Screws out, toothpicks in.

3/8" roundover again - followed by the angle
grinder and sander.

I just 'glassed the corners - using 12
oz biaxial 6" wide tape from Duckworks. 6 oz would have
been much more appropriate, but 12 oz is what I had.

There we go.

Time to roll her over. Mike L had stopped by for a
visit, so I got to be the photographer while he and Geoff did the
work.

That little round thing is the reinforcement for the
bow eye.

We put up some temporary bracing to keep the sides
true and keep twist out.

Instead of keeping it simple, we were going to see
if we could so a small cuddy with a curved top for the foredeck.
It was touch and go for a while - I was constantly tempted to just
cut it off flush, but Geoff is a good craftsman and went to work
on the curved deck beams.

While Geoff worked on the deck beams, I installed
the airbox bulkheads.

Deck beams temporarily held in place, it was time
to figure out the mast rake and placement. I have no idea what I'm
doing.

My mast step - there'll be a 3/8 bolt through the
middle there and a notch on the bottom of the mast.

Another coat of epoxy before the decks go on.

OK, deck beams in place, mast step and partner are
in place, looks like time to put it all together.

Dry fit the side decks

Dry-fit the fore and aft decks.

Rann stopped by so I put him on making the rudderhead.

Checking final fit.

I believe in painting the insides of airboxes, so tape tape and
more tape.

Easier to paint before the decks are on.

These gudgeons
from Duckworks are really heavy duty. I wanted them installed
before I'd have to crawl under the aft deck.

Side decks on

Foredeck

Epoxied. That's purty.

Now it's all together, it's time to start drilling more holes.
Blocks for the downhaul and a cleat for the bleater.

Leeboard in place.

(out of sequence) Rudder checks out

Oh, my, we are getting close now - lashing the sail
to the spars.
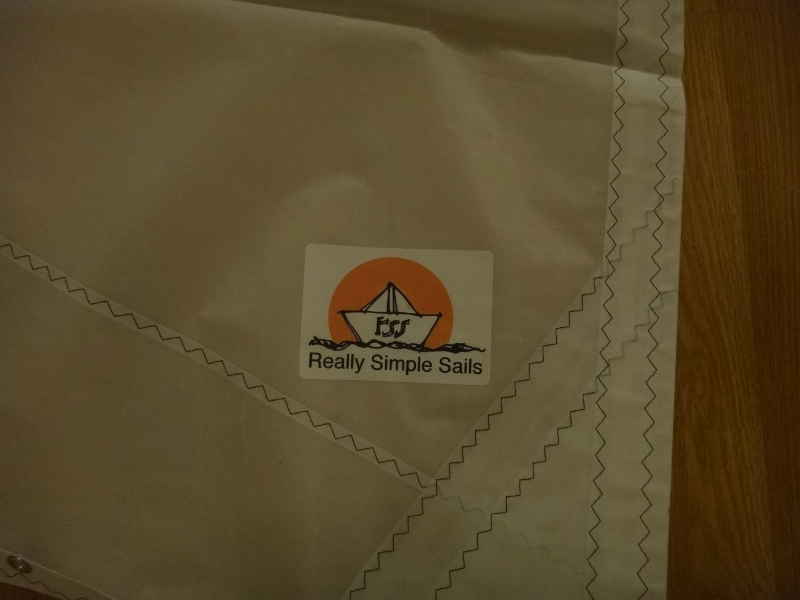
The sail is an 89sqft
Balanced Lug from Really Simple Sails It is EXCELLENT.
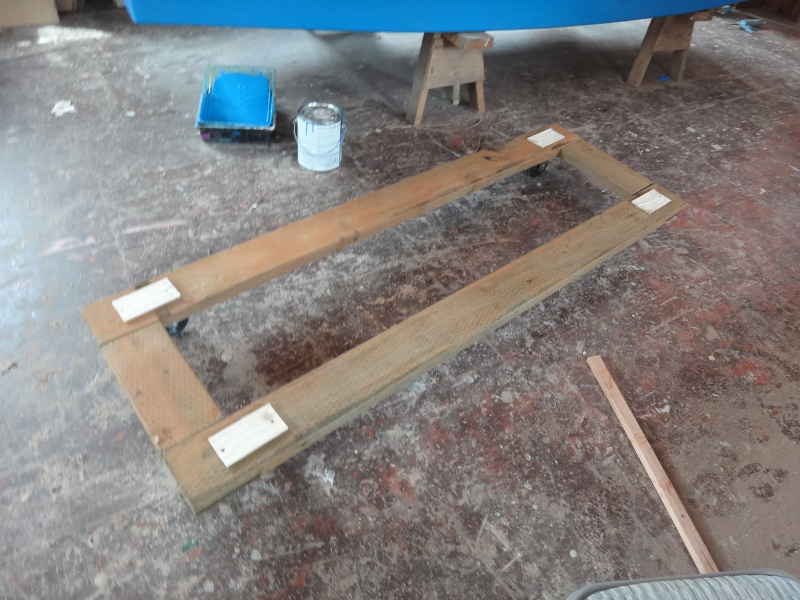
I made a roll around cart to make it easier to maneuver
the boat in the shop.

First time in the sun - and time for us to begin frigging
with the rigging.

I'm lashing the blocks onto the spars - just because
it looks cool.

Launch Day came - the roll around cart came in handy
for getting the boat up to the parking lot.

A very good friend of the Boathouse, Virgil G. gave
me this rigging knife a couple weeks ago. It came in very handy.

Yard sailing - mostly rigged and looking pretty.

She hit the water on April 17, 2015, at the Depoe
Bay Boatshow. I pressed a couple of kids into being crew and sailing
buddy David as helmsman. The wind was blowing very strong and right
in our teeth.

This is a great boat. The kids paddled dead into the
15-20mph wind with relative ease.

I did some final rigging and had some friends around
while she was cast off, under sail, for the first time.

(photo credit: John Kohnen) Oh, she sails sweet. Really
skims along. Well balanced and smooth.

And now with a crew of five. I need to shorten the
tiller to give us more options for trim - five is a little crowded.
|