Family Boat Build at the Toledo
Community Boathouse
Preparation
Sometime in the summer of 2011, we decided the
Boathouse needed an event - a BIG event - to keep things moving
over the winter. We figured winter was a good time for boat
building, so we decided to do a Family Boat Build.
After much deliberation we chose to do a Skin-on-Frame
(SoF) build. SoF technology requires a LOT of preparation,
but once you have the strongbacks, frames, stems, stringers,
and keels cut, sanded, and treated, the actual building of
the boat is mostly tying knots and making cuts with hand saws
- skills easily taught to neophytes. No toxic glues, very
little use of power tools, and the boats look fantastic.
We decided on a design by Dave Gentry, of Gentry
Custom Boats, and he supplied the initial design to us,
donating his licensing fee. We then modified the design slightly
to better fit our desires.
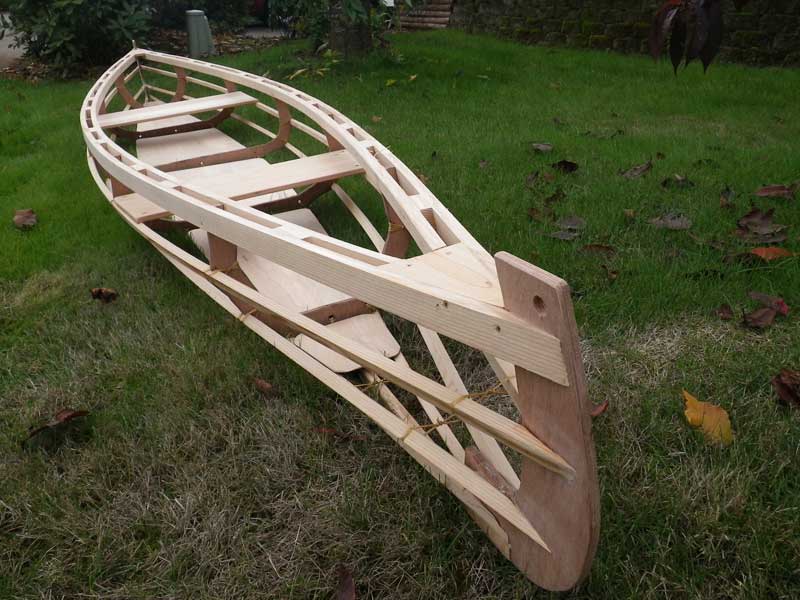
We built a prototype because it is easier to
show people what we wanted to do rather than explain it. This
gave us an excellent idea of the Bill of Materials, along
with time-to-complete estimates.
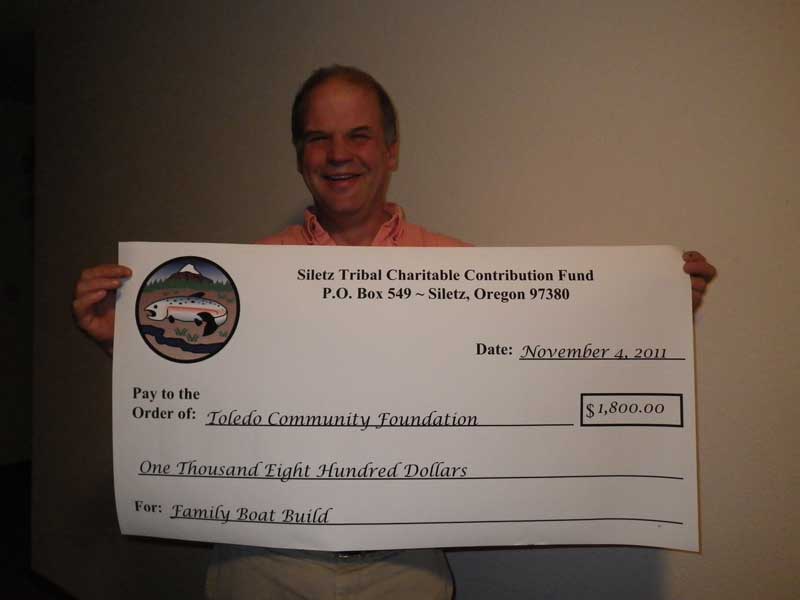
We put together a budget and submitted a grant
request to the Confederated Tribes of the Siletz Indians.
Amazingly, it was approved. All we had to do now was get ready.
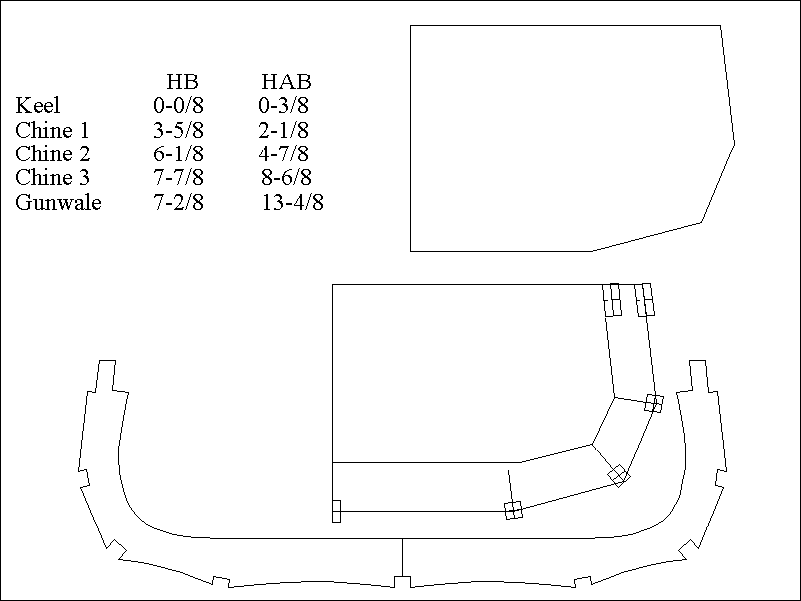
Dave had given me a list of offsets for the
canoe design (the blob of numbers in the upper left) I put
them into my drawing program to get the cross section of the
boat at that point (upper right) then worked up the design
of the frame that would go there (middle and bottom.) Once
that was done, it was off to Kinko's to get a full-sized template
printed up.
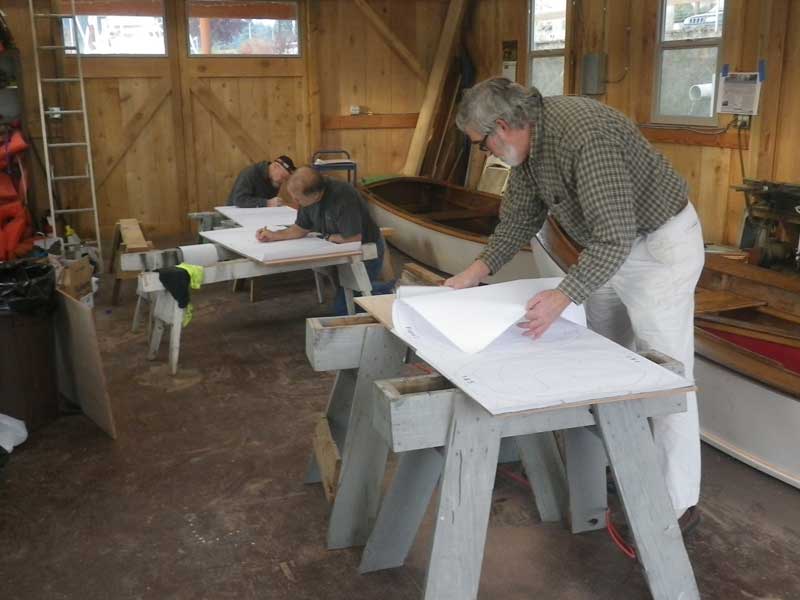
By carefully laying out the frames on the template,
we were able to fit all five frames and both stems into a
2x4 piece of plywood - four boats from one sheet of 1/2"
marine ply. Curt, Jim and I covered the plywood with carbon
paper, pinned down the template, and traced out the shapes
of the frames.
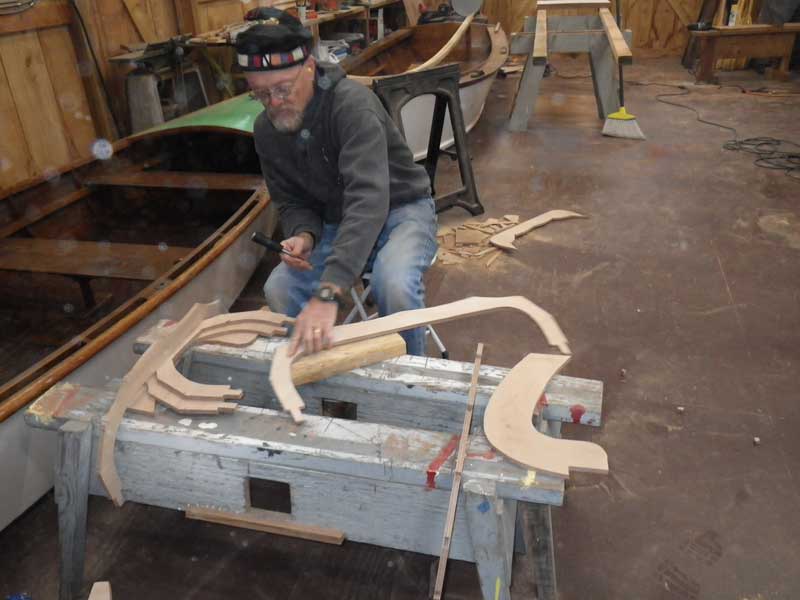
Cutting the frames and stems was tedious, was
but it went by quick enough.
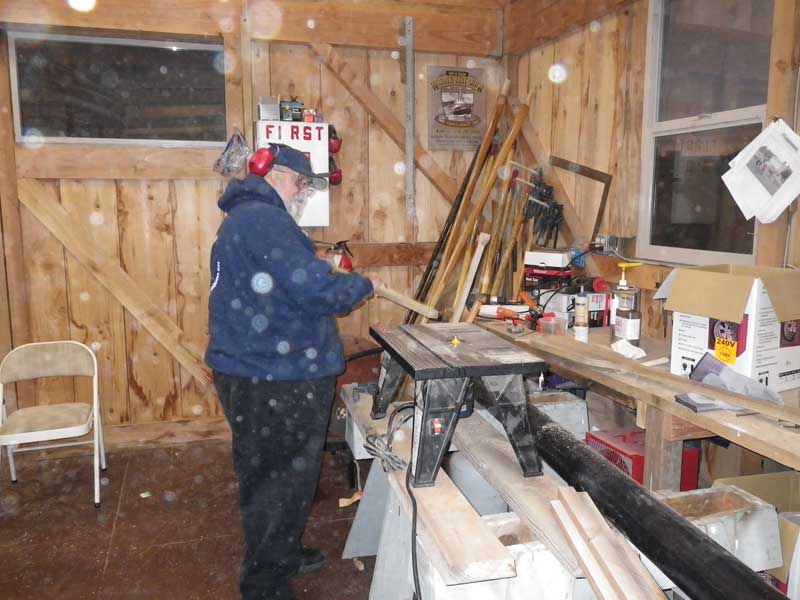
The final step was running all 28 pieces through
a router with a 3/16 roundover bit. Frank did that for us.
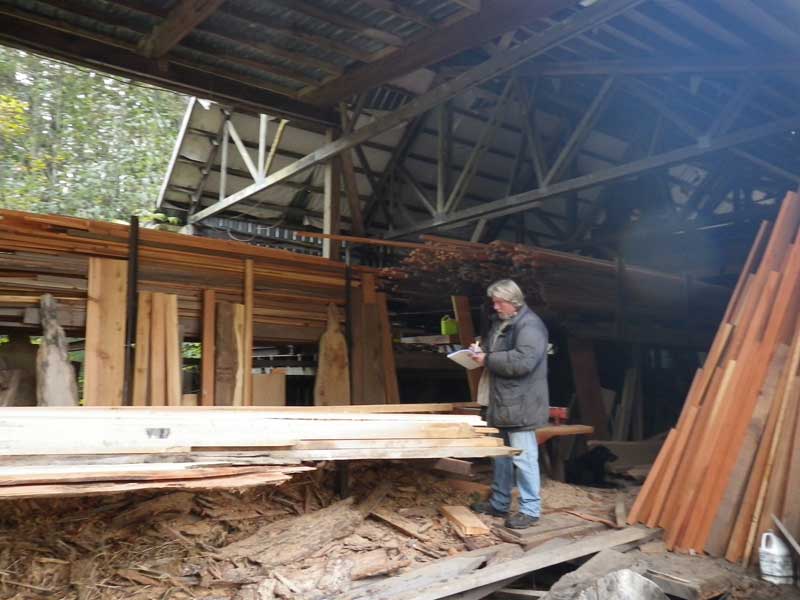
In addition to the five frames, two stems, and
six floorboards (not show) for each boat, we also needed 16'
long pieces of clear timber - specifically four 1x2s for the
wales, six 1x1s for the stringers, and a 1-1/4x1 for the keel.
For this, we went out to Siletz River Timber company and were
allowed to root through their piles.
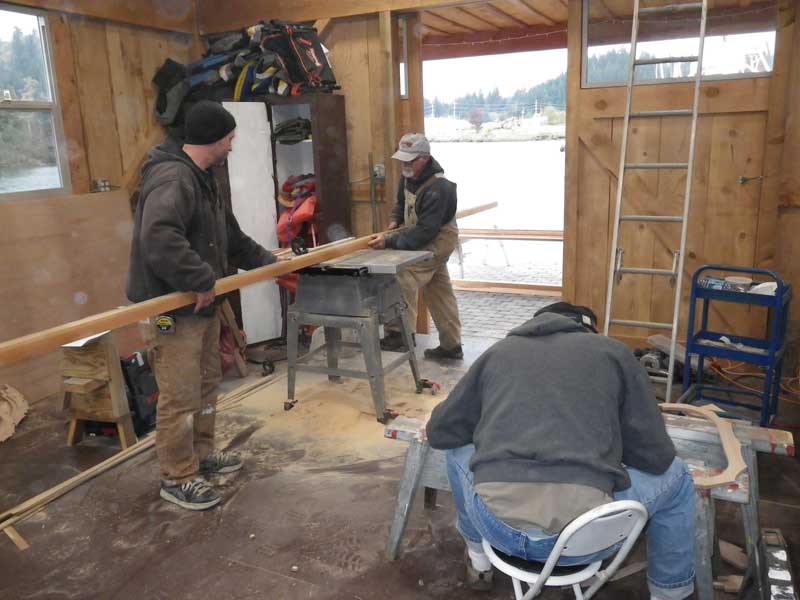
We got rough-cut timbers and had to rip 'em
down to size. Rick and Aaron did the lion's share of that
work. Then we planed 'em smooth and sanded each piece to take
the sharp corners off.
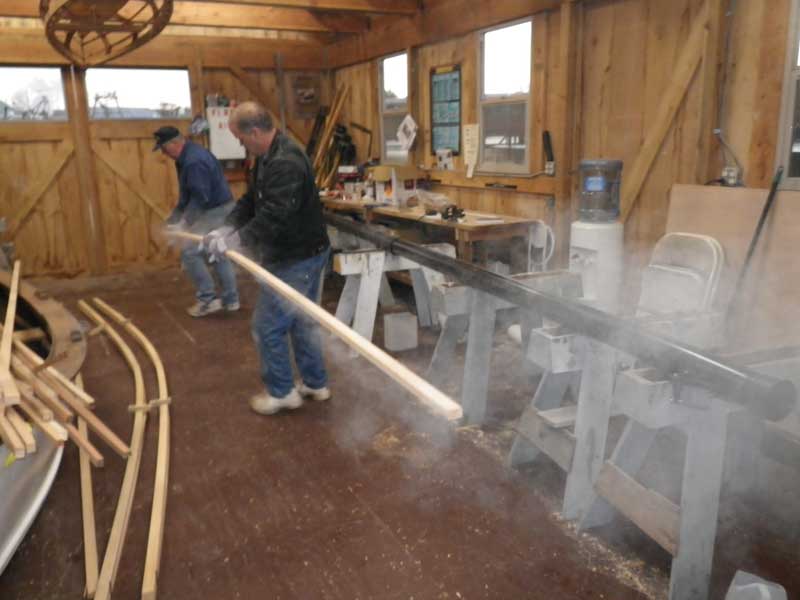
To make sure the boats would hold their shape,
we had to learn how to steam bend. Chuck helped out as we
borrowed Rick's steamer and did all the Wales and some other
bits.
After we had all the pieces, we coated each
of them with at least two coats of Varathane to seal them.
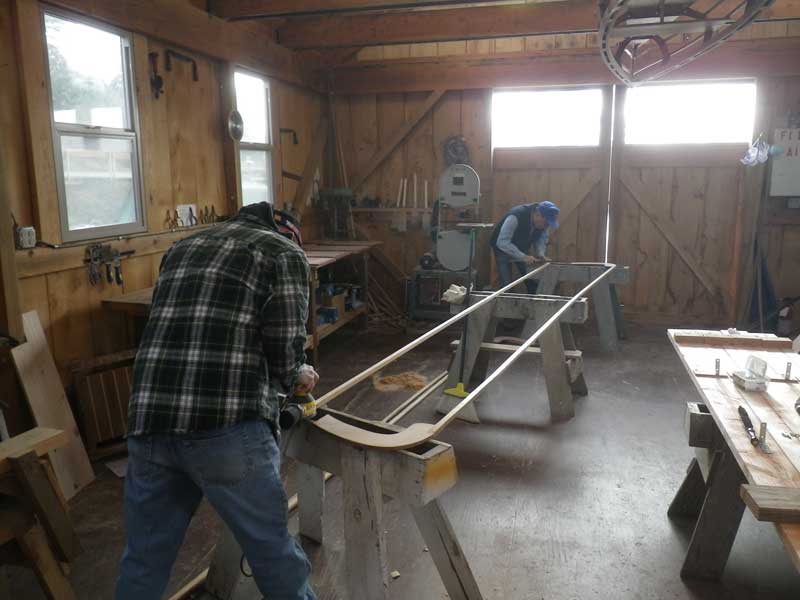
The final step of preparation was for Dave and
Curt to attach the stems to the keels and set them up the
strongbacks.
This essay doesn't show the rest of the "behind
the scenes" operations: ordering the 8 oz polyester that
will be the skin, the artificial sinew, buying the screws
and "L" brackets for the strongbacks, driving all
over the Willamette Valley to get the plywood, hot knives,
heat guns, etc. etc.
This ended up being an enormous amount of effort
- especially for an all-volunteer organization like ours.
Did it end up being worth it? Yep, I can say it was, without
a doubt.
|